SMT utilizza l'analisi e la soluzione convenzionali della cavità di saldatura a riflusso dell'aria con pasta saldante (edizione Essence 2023), te lo meriti!
1 Introduzione

Nell'assemblaggio della scheda del circuito, la pasta saldante viene prima stampata sul pad di saldatura del circuito, quindi vengono fissati i vari componenti elettronici. Infine, dopo il forno a rifusione, le gocce di stagno nella pasta saldante vengono fuse e tutti i tipi di componenti elettronici e il pad di saldatura del circuito stampato vengono saldati insieme per realizzare l'assemblaggio dei sottomoduli elettrici. la tecnologia a montaggio superficiale (sMT) è sempre più utilizzata nei prodotti di imballaggio ad alta densità, come i pacchetti a livello di sistema (siP), i dispositivi ballgridarray (BGA) e Power Bare Chip, pacchetto quadrato piatto senza pin (quad aatNo-lead, denominato QFN ) dispositivo.
A causa delle caratteristiche del processo e dei materiali di saldatura della pasta saldante, dopo la saldatura a rifusione di questi dispositivi con superficie di saldatura di grandi dimensioni, saranno presenti dei fori nell'area di saldatura, che influenzeranno le proprietà elettriche, le proprietà termiche e le proprietà meccaniche delle prestazioni del prodotto, e portare anche al guasto del prodotto, quindi, per migliorare la cavità di saldatura a riflusso della pasta saldante è diventato un processo e un problema tecnico che deve essere risolto, alcuni ricercatori hanno analizzato e studiato le cause della cavità di saldatura della sfera di saldatura BGA e hanno fornito soluzioni di miglioramento, saldatura convenzionale area di saldatura del processo di saldatura a rifusione della pasta Manca QFN maggiore di 10 mm2 o area di saldatura maggiore di 6 mm2. Manca la soluzione a truciolo nudo.
Utilizzare la saldatura preformata e la saldatura in forno a riflusso sotto vuoto per migliorare il foro di saldatura. La saldatura prefabbricata richiede attrezzature speciali per puntare il flusso. Ad esempio, il chip viene spostato e inclinato notevolmente dopo essere stato posizionato direttamente sulla saldatura prefabbricata. Se il chip di montaggio del flusso viene rifuso e quindi puntato, il processo viene aumentato di due riflussi e il costo della saldatura prefabbricata e del materiale di flusso è molto più elevato rispetto alla pasta saldante.
L'attrezzatura per il riflusso del vuoto è più costosa, la capacità del vuoto della camera del vuoto indipendente è molto bassa, il rapporto costi-prestazioni non è elevato e il problema degli spruzzi di stagno è serio, il che è un fattore importante nell'applicazione di alta densità e passo piccolo prodotti. In questo documento, basato sul processo di saldatura a rifusione convenzionale della pasta saldante, viene sviluppato e introdotto un nuovo processo di saldatura a rifusione secondaria per migliorare la cavità di saldatura e risolvere i problemi di incollaggio e di rottura delle guarnizioni di plastica causate dalla cavità di saldatura.
2 Cavità di saldatura a riflusso per stampa di pasta saldante e meccanismo di produzione
2.1 Cavità di saldatura
Dopo la saldatura a rifusione, il prodotto è stato testato ai raggi X. I fori nella zona di saldatura con colore più chiaro sono risultati dovuti a una saldatura insufficiente nello strato di saldatura, come mostrato nella Figura 1
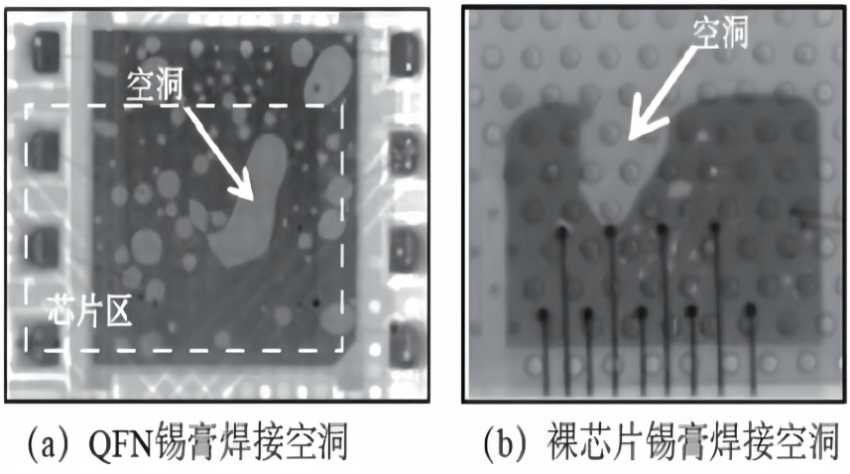
Rilevamento a raggi X del foro della bolla
2.2 Meccanismo di formazione della cavità di saldatura
Prendendo come esempio la pasta saldante sAC305, la composizione e la funzione principali sono mostrate nella Tabella 1. Il fondente e le perle di stagno sono legati insieme sotto forma di pasta. Il rapporto in peso tra stagno e flusso è di circa 9:1 e il rapporto in volume è di circa 1:1.
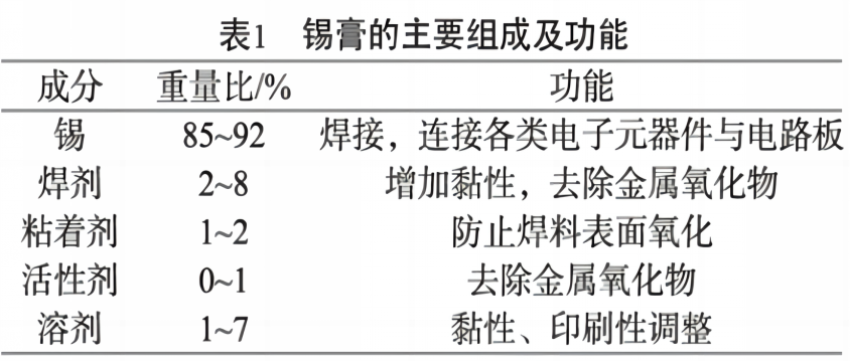
Dopo che la pasta saldante è stata stampata e montata con vari componenti elettronici, la pasta saldante subirà quattro fasi di preriscaldamento, attivazione, riflusso e raffreddamento quando passa attraverso il forno di riflusso. Anche lo stato della pasta saldante è diverso con temperature diverse nelle diverse fasi, come mostrato nella Figura 2.
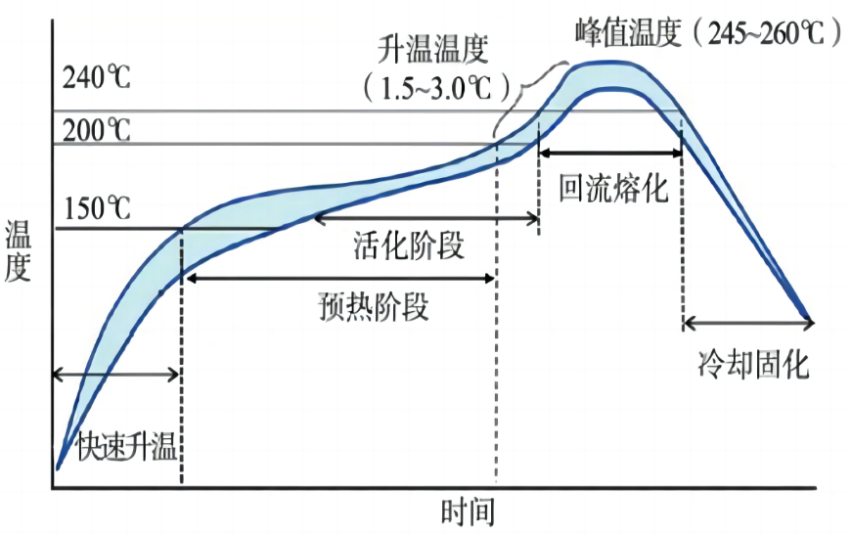
Riferimento del profilo per ciascuna area di saldatura a rifusione
Nella fase di preriscaldamento e attivazione, i componenti volatili nel flusso nella pasta saldante verranno volatilizzati in gas una volta riscaldati. Allo stesso tempo, quando viene rimosso l'ossido sulla superficie dello strato di saldatura, verranno prodotti gas. Alcuni di questi gas si volatilizzeranno e lasceranno la pasta saldante e i cordoni di saldatura saranno strettamente condensati a causa della volatilizzazione del flusso. Nella fase di riflusso, il flusso rimanente nella pasta saldante evaporerà rapidamente, le perle di stagno si scioglieranno, una piccola quantità di gas volatile del flusso e la maggior parte dell'aria tra le perle di stagno non verranno disperse nel tempo e il residuo nella pasta saldante lo stagno fuso e sotto la tensione dello stagno fuso sono una struttura a sandwich di hamburger e vengono catturati dal pad di saldatura del circuito stampato e dai componenti elettronici, e il gas avvolto nello stagno liquido è difficile fuoriuscire solo dalla galleggiabilità verso l'alto Il tempo di fusione superiore è molto corto. Quando lo stagno fuso si raffredda e diventa stagno solido, nello strato di saldatura compaiono pori e si formano fori di saldatura, come mostrato nella Figura 3.
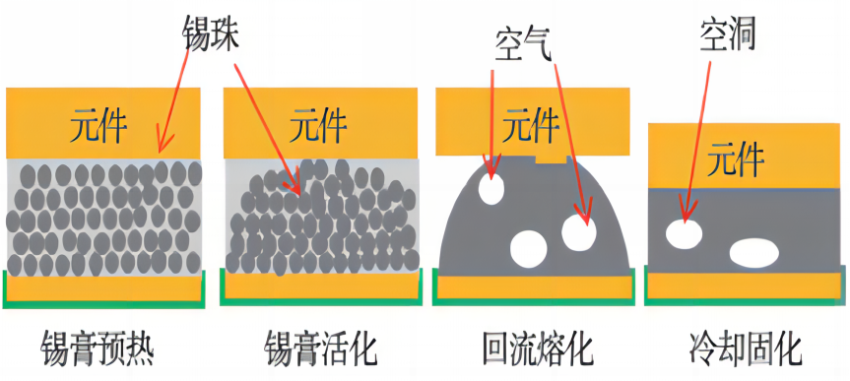
Diagramma schematico del vuoto generato dalla saldatura a rifusione della pasta saldante
La causa principale della cavità di saldatura è che l'aria o il gas volatile avvolti nella pasta saldante dopo la fusione non vengono scaricati completamente. I fattori che influenzano includono il materiale della pasta saldante, la forma di stampa della pasta saldante, la quantità di stampa della pasta saldante, la temperatura di riflusso, il tempo di riflusso, le dimensioni della saldatura, la struttura e così via.
3. Verifica dei fattori che influenzano la stampa della pasta saldante sui fori di saldatura a rifusione
I test QFN e su chip nudo sono stati utilizzati per confermare le cause principali dei vuoti di saldatura a rifusione e per trovare modi per migliorare i vuoti di saldatura a rifusione stampati con pasta saldante. Il profilo del prodotto per la saldatura a riflusso di pasta saldante QFN e chip nudo è mostrato nella Figura 4, la dimensione della superficie di saldatura QFN è 4,4 mm x 4,1 mm, la superficie di saldatura è uno strato stagnato (stagno puro al 100%); La dimensione di saldatura del chip nudo è 3,0 mm x 2,3 mm, lo strato di saldatura è uno strato bimetallico di nichel-vanadio spruzzato e lo strato superficiale è di vanadio. Il tampone di saldatura del substrato era rivestito in oro per immersione chimica in nichel-palladio e lo spessore era di 0,4μm/0,06μm/0,04μm. Viene utilizzata la pasta saldante SAC305, l'attrezzatura per la stampa della pasta saldante è DEK Horizon APix, l'attrezzatura del forno a riflusso è BTUPyramax150N e l'attrezzatura a raggi X è DAGExD7500VR.
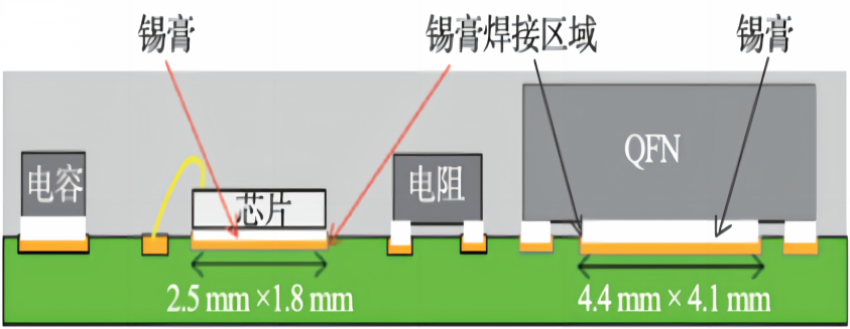
Disegni di saldatura QFN e truciolo nudo
Per facilitare il confronto dei risultati dei test, la saldatura a rifusione è stata eseguita nelle condizioni riportate nella Tabella 2.
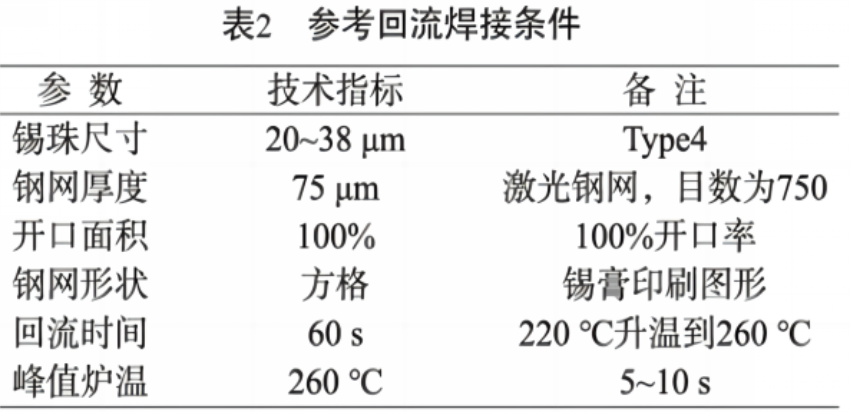
Tabella delle condizioni di saldatura a rifusione
Dopo aver completato il montaggio superficiale e la saldatura a rifusione, lo strato di saldatura è stato rilevato dai raggi X e si è riscontrato che erano presenti grandi fori nello strato di saldatura sul fondo del QFN e nel chip nudo, come mostrato nella Figura 5.
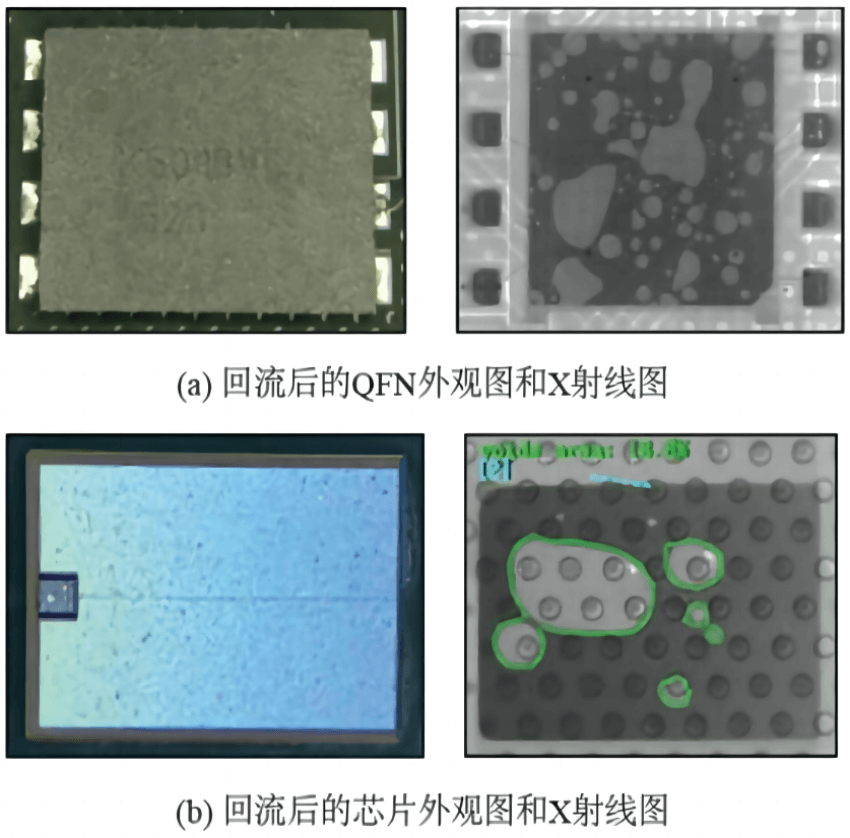
QFN e ologramma del chip (raggi X)
Poiché le dimensioni del cordone di stagno, lo spessore della rete di acciaio, il tasso di apertura, la forma della rete di acciaio, il tempo di riflusso e la temperatura di picco del forno influenzeranno tutti i vuoti di saldatura a rifusione, ci sono molti fattori che influenzano, che saranno verificati direttamente dal test DOE, e il numero di prove sperimentali i gruppi saranno troppo grandi. È necessario vagliare e determinare rapidamente i principali fattori d'influenza tramite il test comparativo di correlazione, quindi ottimizzare ulteriormente i principali fattori d'influenza tramite DOE.
3.1 Dimensioni dei fori di saldatura e dei cordoni di stagno della pasta saldante
Con il test della pasta saldante SAC305 di tipo 3 (dimensione del cordone 25-45 μm), le altre condizioni rimangono invariate. Dopo la rifusione, i fori nello strato saldante vengono misurati e confrontati con la pasta saldante di tipo 4. Si è riscontrato che i fori nello strato saldante non sono significativamente diversi tra i due tipi di pasta saldante, indicando che la pasta saldante con dimensioni diverse del cordone non ha un'influenza evidente sui fori nello strato saldante, il che non è un fattore influente, come mostrato nella FIG. 6 Come mostrato.
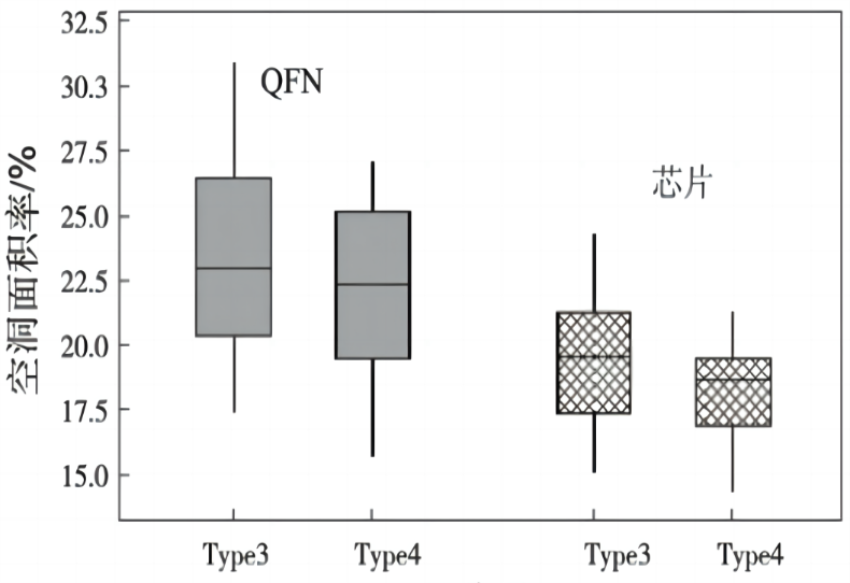
Confronto tra fori di polvere di stagno metallico con particelle di diverse dimensioni
3.2 Spessore della cavità di saldatura e della rete di acciaio stampata
Dopo la rifusione, l'area della cavità dello strato saldato è stata misurata con la rete di acciaio stampata dello spessore di 50 μm, 100 μm e 125 μm e le altre condizioni sono rimaste invariate. Si è riscontrato che l'effetto del diverso spessore della rete di acciaio (pasta saldante) sul QFN è stato confrontato con quello della rete di acciaio stampata con uno spessore di 75 μm. All'aumentare dello spessore della rete di acciaio, l'area della cavità diminuisce gradualmente e lentamente. Dopo aver raggiunto un certo spessore (100μm), l'area della cavità si invertirà e inizierà ad aumentare con l'aumento dello spessore della rete di acciaio, come mostrato nella Figura 7.
Ciò dimostra che quando si aumenta la quantità di pasta saldante, lo stagno liquido con riflusso viene coperto dal chip e l'uscita dell'aria residua è stretta solo su quattro lati. Quando si cambia la quantità di pasta saldante, viene aumentata anche l'uscita dell'aria residua e l'esplosione istantanea di aria avvolta nello stagno liquido o nel gas volatile che fuoriesce dallo stagno liquido causerà schizzi di stagno liquido attorno al QFN e al chip.
Il test ha rilevato che con l'aumento dello spessore della rete di acciaio, aumenterà anche lo scoppio delle bolle causato dalla fuga di aria o gas volatile e aumenterà corrispondentemente anche la probabilità che lo stagno schizzi intorno a QFN e al chip.
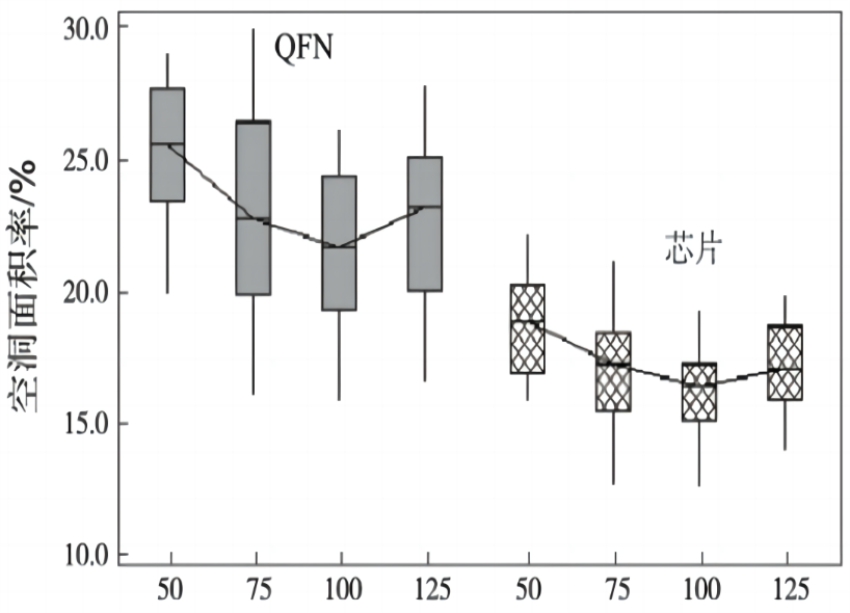
Confronto di fori in maglie di acciaio di diverso spessore
3.3 Rapporto tra le aree della cavità di saldatura e dell'apertura della rete di acciaio
È stata testata la rete di acciaio stampata con un tasso di apertura del 100%, 90% e 80% e le altre condizioni sono rimaste invariate. Dopo la rifusione, l'area della cavità dello strato saldato è stata misurata e confrontata con la rete di acciaio stampata con un tasso di apertura del 100%. Si è riscontrato che non vi era alcuna differenza significativa nella cavità dello strato saldato nelle condizioni di velocità di apertura del 100% e 90% 80%, come mostrato nella Figura 8.
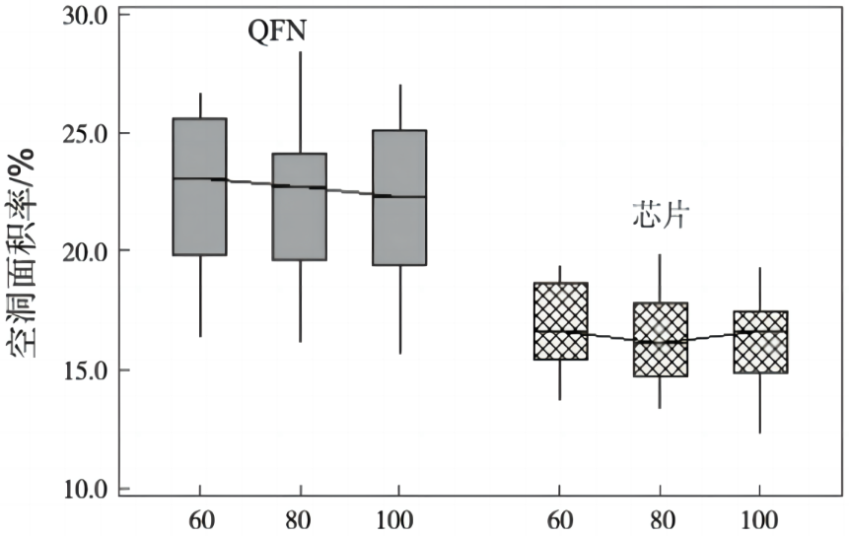
Confronto delle cavità di diverse aree di apertura di diverse maglie di acciaio
3.4 Cavità saldata e forma della rete di acciaio stampata
Con la prova della forma di stampa della pasta saldante della striscia b e della griglia inclinata c, le altre condizioni rimangono invariate. Dopo la rifusione, l'area della cavità dello strato di saldatura viene misurata e confrontata con la forma di stampa della griglia a. Si riscontra che non vi è alcuna differenza significativa nella cavità dello strato di saldatura nelle condizioni di griglia, striscia e griglia inclinata, come mostrato in Figura 9.
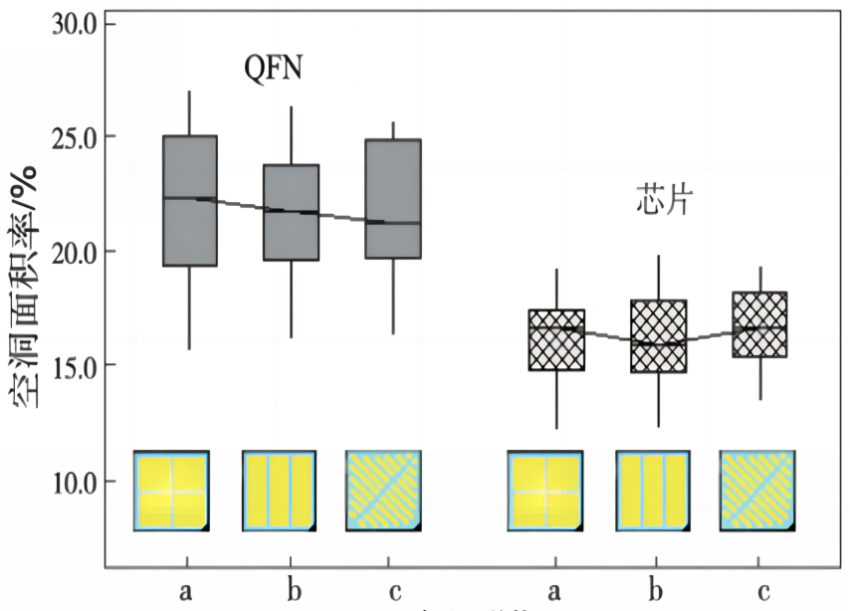
Confronto dei fori nelle diverse modalità di apertura della rete d'acciaio
3.5 Cavità di saldatura e tempo di riflusso
Dopo un test del tempo di riflusso prolungato (70 s, 80 s, 90 s), le altre condizioni rimangono invariate, il foro nello strato di saldatura è stato misurato dopo il riflusso e, confrontato con il tempo di riflusso di 60 s, si è riscontrato che con l'aumento di tempo di riflusso, l'area del foro di saldatura è diminuita, ma l'ampiezza della riduzione è gradualmente diminuita con l'aumento del tempo, come mostrato nella Figura 10. Ciò mostra che in caso di tempo di riflusso insufficiente, aumentando il tempo di riflusso il tempo di riflusso favorisce il pieno trabocco dell'aria avvolta nello stagno liquido fuso, ma dopo che il tempo di riflusso aumenta fino a un certo tempo, è difficile che l'aria avvolta nello stagno liquido trabocchi nuovamente. Il tempo di riflusso è uno dei fattori che influenzano la cavità di saldatura.
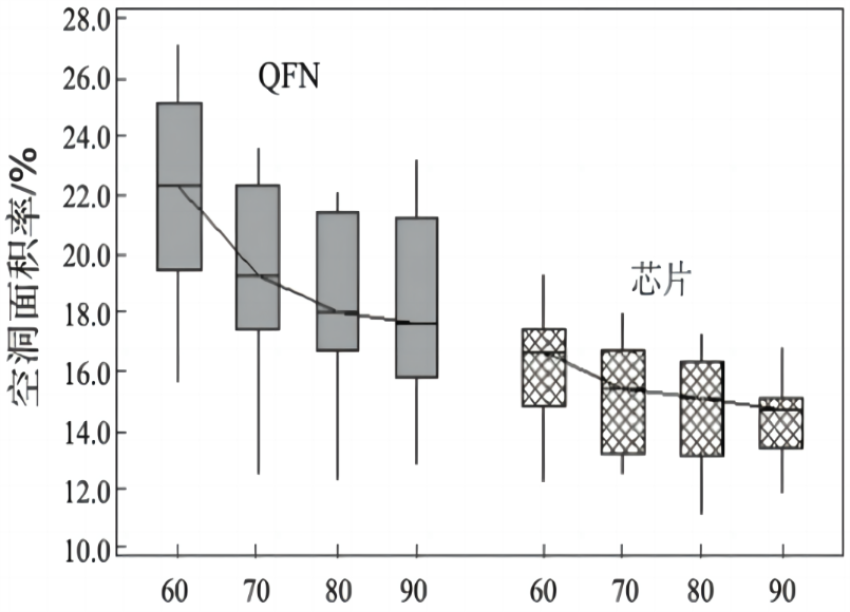
Confronto vuoto di diverse durate di tempo di reflusso
3.6 Cavità di saldatura e temperatura di punta del forno
Con il test della temperatura di picco del forno di 240 ℃ e 250 ℃ e altre condizioni invariate, l'area della cavità dello strato saldato è stata misurata dopo la rifusione e, rispetto alla temperatura di picco del forno di 260 ℃, si è scoperto che in diverse condizioni di temperatura di picco del forno, la cavità di lo strato saldato di QFN e il chip non è cambiato in modo significativo, come mostrato nella Figura 11. Mostra che la diversa temperatura di picco del forno non ha effetti evidenti su QFN e sul foro nello strato di saldatura del chip, che non è un fattore influente.
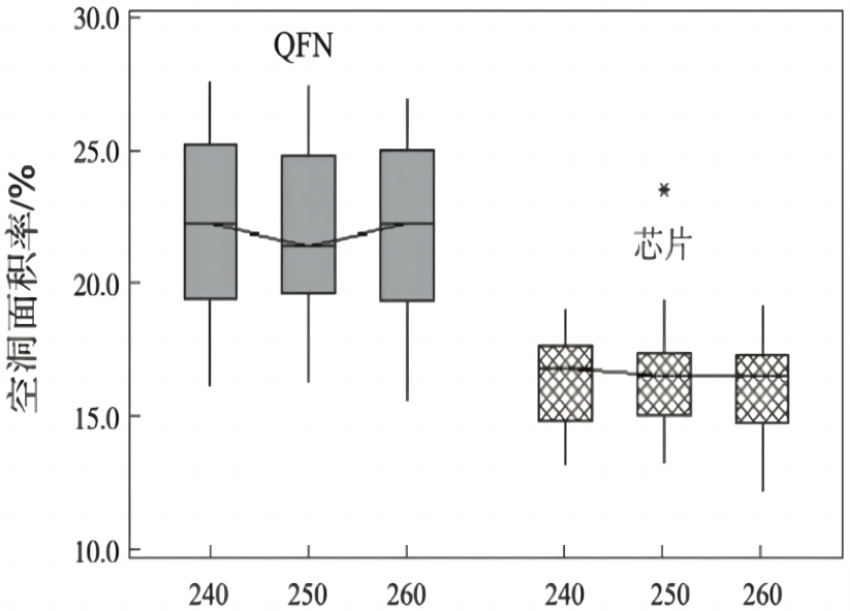
Confronto vuoto di diverse temperature di picco
I test di cui sopra indicano che i fattori significativi che influenzano la cavità dello strato saldato di QFN e il truciolo sono il tempo di riflusso e lo spessore della rete di acciaio.
4 Miglioramento della cavità di saldatura a rifusione della stampa della pasta saldante
4.1 Test DOE per migliorare la cavità di saldatura
Il foro nello strato di saldatura di QFN e truciolo è stato migliorato trovando il valore ottimale dei principali fattori d'influenza (tempo di riflusso e spessore della rete di acciaio). La pasta saldante era di tipo SAC3054, la forma della maglia di acciaio era del tipo a griglia (grado di apertura del 100%), la temperatura di picco del forno era di 260 ℃ e le altre condizioni di test erano le stesse dell'attrezzatura di prova. Il test DOE e i risultati sono stati mostrati nella Tabella 3. Le influenze dello spessore della rete di acciaio e del tempo di riflusso sul QFN e sui fori di saldatura del truciolo sono mostrati nella Figura 12. Attraverso l'analisi dell'interazione dei principali fattori che influenzano, si è riscontrato che utilizzando uno spessore della rete di acciaio di 100 μm e il tempo di riflusso di 80 s può ridurre significativamente la cavità di saldatura di QFN e truciolo. Il tasso di cavità di saldatura di QFN è ridotto dal 27,8% massimo al 16,1% e il tasso di cavità di saldatura del truciolo è ridotto dal 20,5% massimo al 14,5%.
Nel test, 1000 prodotti sono stati realizzati in condizioni ottimali (spessore della rete di acciaio di 100 μm, tempo di riflusso di 80 s) e la velocità della cavità di saldatura di 100 QFN e del truciolo è stata misurata in modo casuale. Il tasso medio di cavità di saldatura di QFN era del 16,4% e il tasso medio di cavità di saldatura del chip era del 14,7%. Il tasso di cavità di saldatura del chip e del chip sono ovviamente ridotti.
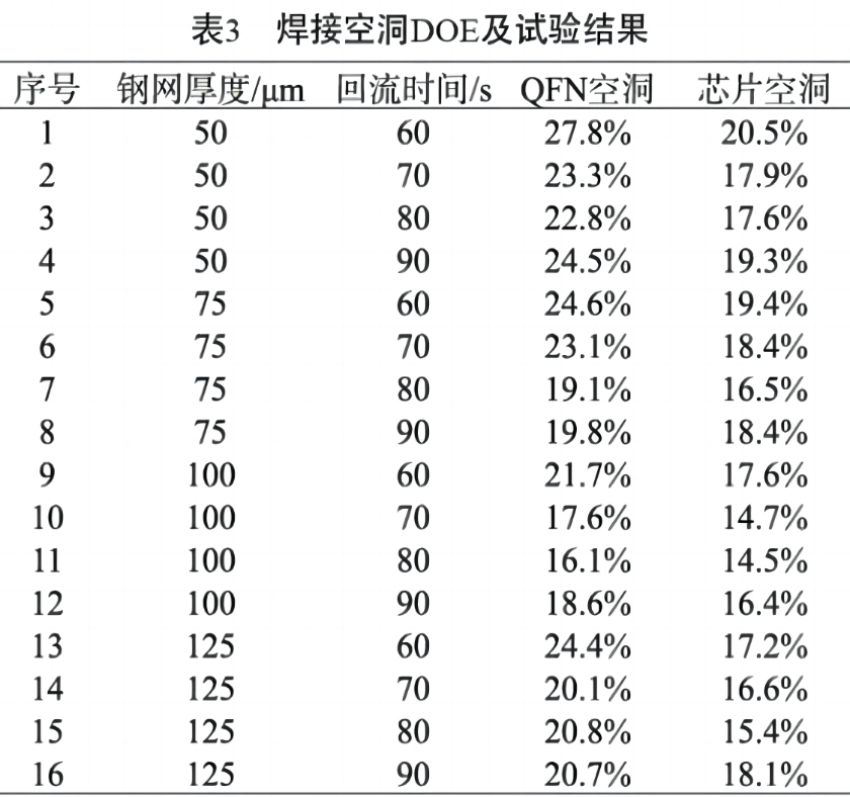
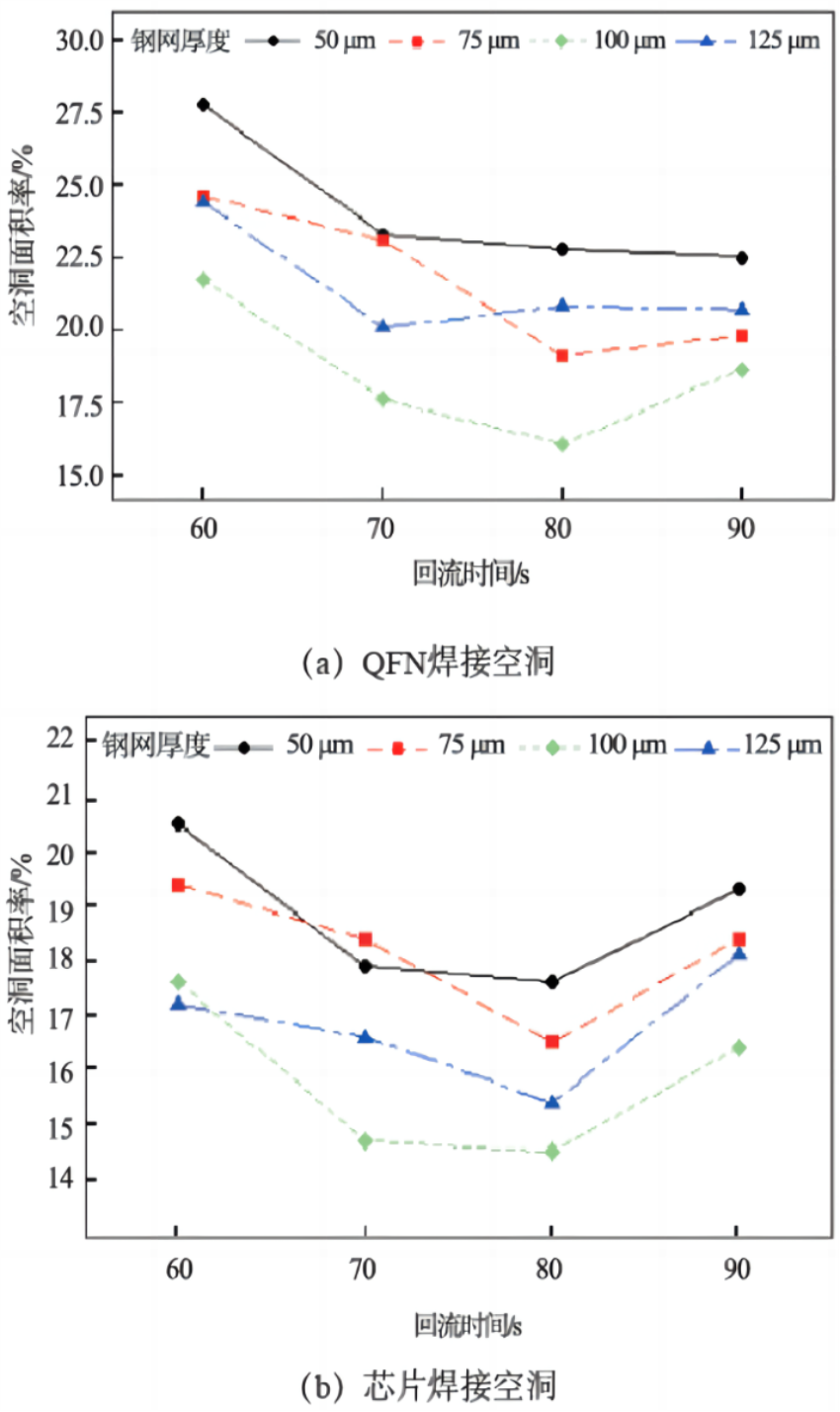
4.2 Il nuovo processo migliora la cavità di saldatura
La situazione di produzione effettiva e i test mostrano che quando l'area della cavità di saldatura sul fondo del chip è inferiore al 10%, il problema della rottura della posizione della cavità del chip non si verificherà durante l'incollaggio e lo stampaggio del piombo. I parametri di processo ottimizzati dal DOE non possono soddisfare i requisiti di analisi e risoluzione dei buchi nella saldatura a rifusione della pasta saldante convenzionale e la velocità dell'area della cavità di saldatura del chip deve essere ulteriormente ridotta.
Poiché il chip ricoperto dalla saldatura impedisce la fuoriuscita del gas nella saldatura, il tasso di fori sul fondo del chip viene ulteriormente ridotto eliminando o riducendo il gas rivestito dalla saldatura. Viene adottato un nuovo processo di saldatura a rifusione con due stampe di pasta saldante: una stampa di pasta saldante, una a rifusione che non copre QFN e chip nudo che scarica il gas nella saldatura; Il processo specifico di stampa della pasta saldante secondaria, patch e riflusso secondario è mostrato nella Figura 13.
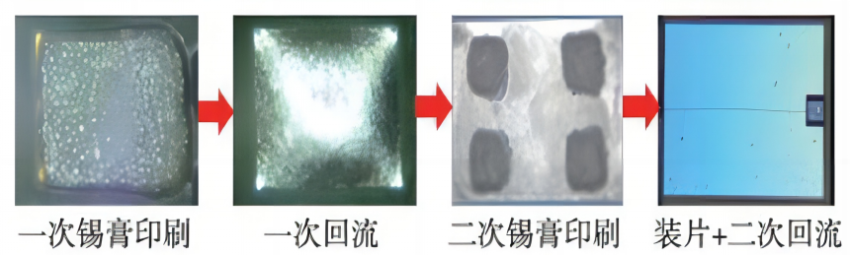
Quando la pasta saldante spessa 75μm viene stampata per la prima volta, la maggior parte del gas nella saldatura senza copertura del truciolo fuoriesce dalla superficie e lo spessore dopo il riflusso è di circa 50μm. Dopo il completamento del riflusso primario, sulla superficie della lega saldante solidificata raffreddata vengono stampati dei piccoli quadrati (per ridurre la quantità di pasta saldante, ridurre la quantità di fuoriuscita di gas, ridurre o eliminare gli spruzzi di saldatura) e la pasta saldante con uno spessore di 50 μm (i risultati del test sopra mostrano che 100 μm è il migliore, quindi lo spessore della stampa secondaria è 100 μm.50 μm=50 μm), quindi installare il chip, e poi ritorno attraverso 80 s. Non c'è quasi nessun foro nella saldatura dopo la prima stampa e rifusione, e la pasta saldante nella seconda stampa è piccola e il foro di saldatura è piccolo, come mostrato nella Figura 14.
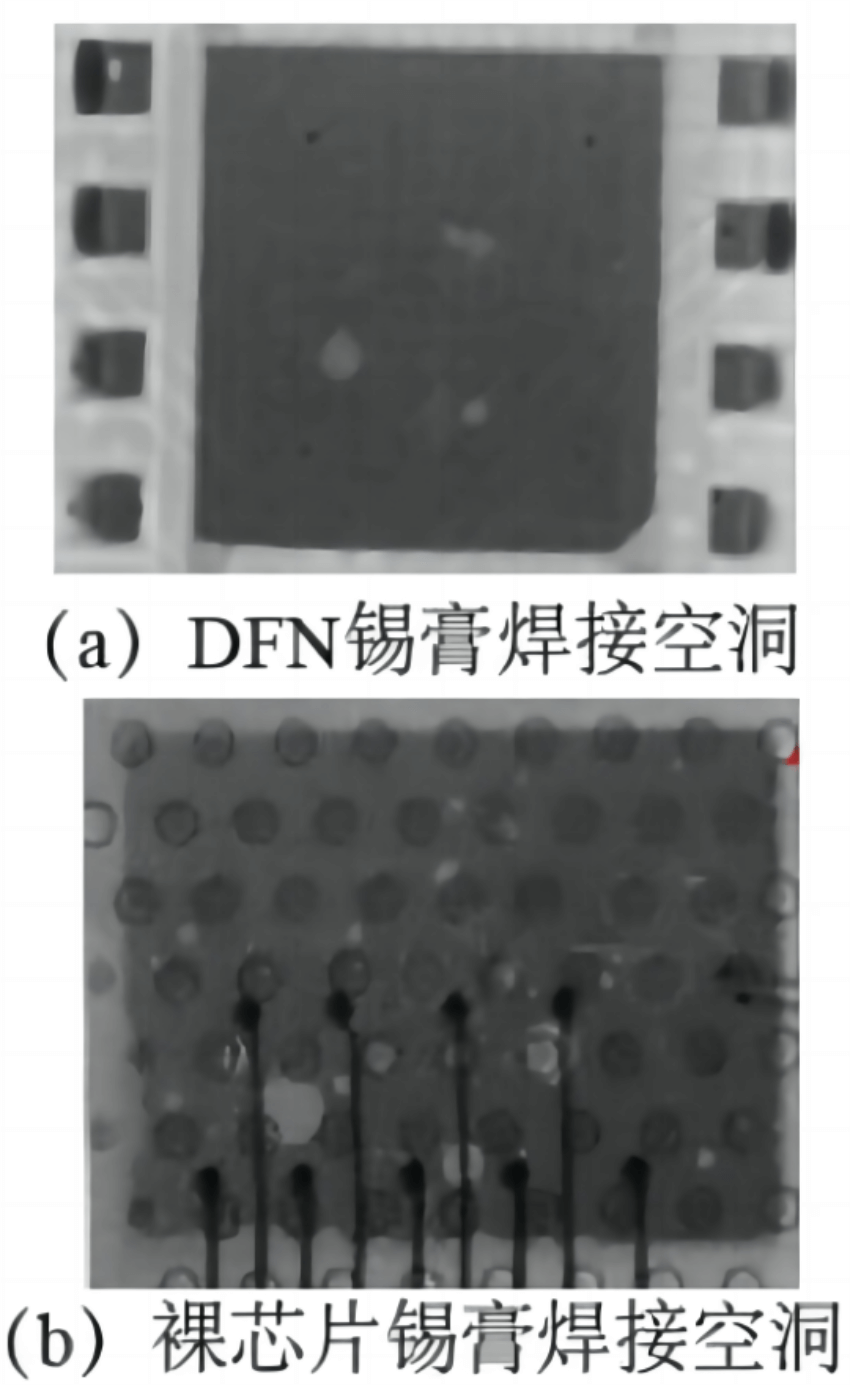
Dopo due stampe di pasta saldante, disegno cavo
4.3 Verifica dell'effetto della cavità di saldatura
Produzione di 2000 prodotti (lo spessore della prima rete di acciaio da stampa è 75 μm, lo spessore della seconda rete di acciaio da stampa è 50 μm), altre condizioni invariate, misurazione casuale di 500 QFN e tasso di cavità di saldatura dei trucioli, ha rilevato che il nuovo processo dopo il primo riflusso nessuna cavità, dopo il secondo riflusso QFN Il tasso massimo di cavità di saldatura è del 4,8% e il tasso massimo di cavità di saldatura del truciolo è del 4,1%. Rispetto al processo di saldatura originale con stampa a pasta singola e al processo ottimizzato DOE, la cavità di saldatura è significativamente ridotta, come mostrato nella Figura 15. Dopo i test funzionali di tutti i prodotti non sono state riscontrate incrinature da truciolo.
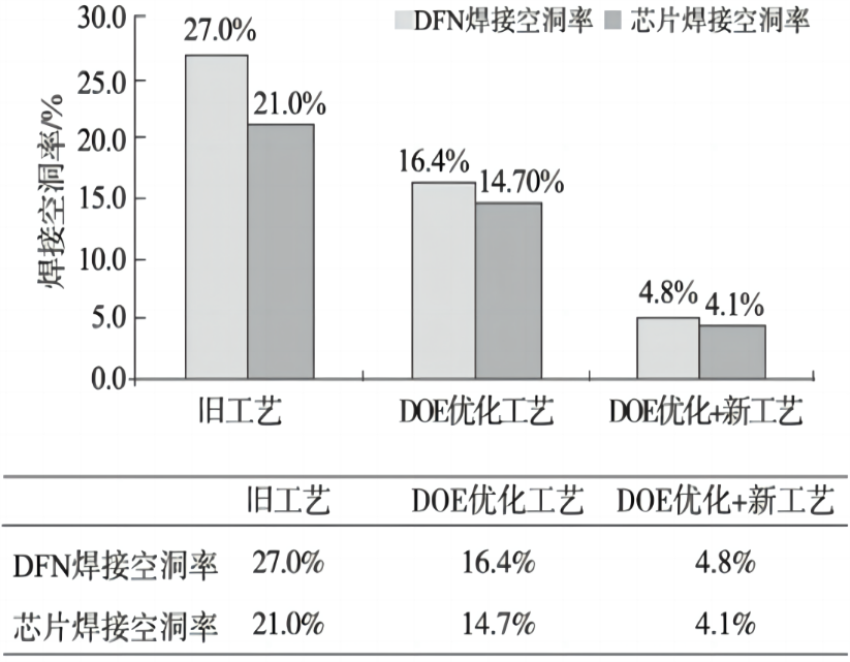
5 Riepilogo
L'ottimizzazione della quantità di stampa della pasta saldante e del tempo di riflusso può ridurre l'area della cavità di saldatura, ma la velocità della cavità di saldatura è ancora elevata. L'utilizzo di due tecniche di saldatura a riflusso con stampa di pasta saldante può massimizzare in modo efficace e massimizzato la velocità della cavità di saldatura. L'area di saldatura del chip nudo del circuito QFN può essere rispettivamente di 4,4 mm x 4,1 mm e 3,0 mm x 2,3 mm nella produzione di massa. La velocità di cavità della saldatura a rifusione è controllata al di sotto del 5%, il che migliora la qualità e l'affidabilità della saldatura a rifusione. La ricerca contenuta in questo documento fornisce un riferimento importante per migliorare il problema della cavità di saldatura di superfici di saldatura di grandi dimensioni.